Expert Structure & Coating Analysis Tool
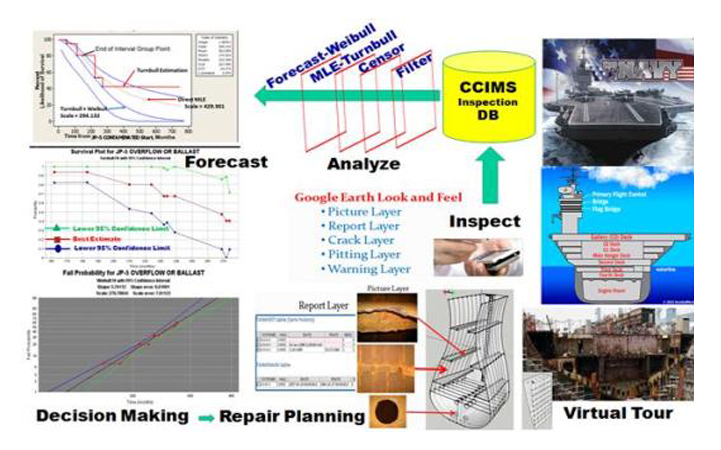
The Navy's war against corrosion is very expensive. A typical Aircraft Carrier has over 600 tanks and voids, which include seawater tanks for ballast and damage control, compensated fuel tanks, fuel/oil service, and potable and water storage tanks. From the material standpoint, the useful life of a ship is ultimately determined by the condition (and corrosion loss) of the internal steel structure. As the fleet ages, coating systems must be replaced as part of the corrosion control effort. Because this coating replacement is difficult and time-consuming, the maintenance of tanks and voids of ships and submarines is one of the highest costs to the Commander's operational budget. Ballast tank inspections alone cost $6K per tank, and 4,000 tanks are inspected annually ($24M/yr). If the ship requires refurbishment of a tank or void, the cost soars to $204M/year because the preparation of the tank for repair is extensive due to safety and the precise environmental constraints imposed for application and adherence of the coating. Frequently, a portion of the ship's hull must be cut open to provide access for workers and equipment.
The GCAS Expert Structures & Coating Analysis Tool (ESCAT) is used by the Navy Carrier Planning Group to automate the inspection, data analysis, and repair process. Data Analytics is used on the resulting inspection database to forecast which tanks will need repair during the next ship availability.
The Tank & Void Corrosion Inspection software contains 3-D models of the tanks, including details such as hatches, ladders, piping, etc, which are prone to corrosion. Using plan views of the different levels within the ship, the software provides a virtual tour of the ship, showing fast and accurate information about the damage observed during inspection. The software features a "Google-Map" type interface using 3-D models for quick retrieval of inspection reports, photos, and voice recordings by clicking on a tank or location within the tank.
The 3-D models are also used by the maintenance and repair crews to plan their work, including estimates of the amount of paint required, communicating the required effort to work crews, and even performing Engineering Finite Element Analysis for structural integrity.
The inspection data is uploaded and stored in the Navy's Corrosion Control Information Management System (CCIMS) database for further analysis to conduct maintenance planning decision-making. ESCAT performs data mining on the CCIMS database of prior inspections and utilizes specialty filtering, data censoring, Turnbull Maximum Likelihood Estimation, and Weibull Reliability Life Forecasting techniques to model the structural deterioration and coating system breakdown over time.
The data is first filtered to select tanks providing similar services on the ship and over the entire fleet. Data containing missing information is corrected or discarded. In order to increase the number of data points to be used in the statistical analysis, special data censoring techniques are used.
Ideally, in order to estimate the mean time to failure, the data would have a time point at which the tank was new and a time point at which failure occurred. With aircraft carrier corrosion, however, the inspections and repairs are only done during in-port ship availabilities, which typically are every 6 to 8 years. Furthermore, a general 1 to 4 rating scale is used to determine if the coating deterioration and subsequent corrosion are bad enough to be called a failure (normally a level "3" on most tanks). The fleet-wide historical database, therefore, contains data where the previous corrosion state before failure is unknown (late entries) or where there has been no failure event since the tank was last refurbished ("loss"). Censoring techniques developed for reliability analysis and forecasting are used to include these points into a non-parametric statistical technique called "Turnbull Maximum Likelihood Estimate" (MLE).
These estimated data points are assembled and faired with a parametric Weibull probability distribution curve fit that is normally used in Engineering reliability and failure analysis. These parametric curves provide the basis for predicting when the different types of service tanks may fail, thereby giving the maintenance and repair planning group the needed forecasting tool for deciding which tanks should be refurbished during the next availability.